Improve Efficiency of Rotational Molding Processes With a Technical Audit
Gaining market share in rotational molding can feel like an uphill battle. Increasingly, molders find themselves competing in a tight market, while navigating disruptions, such as industry consolidation, labor shortages and regional environmental regulations. One way to stay competitive through the ups and downs of business uncertainty is to regularly audit your rotational molding process. A technical audit can help identify areas of improvement, ultimately leading to higher efficiency and lower operating costs.
Product Manager, Bill Christian, who leads M. Holland’s Rotational Molding team, shared his approach to improving efficiency in rotational molding facilities, including the process, benefits and outcomes of conducting a technical audit.
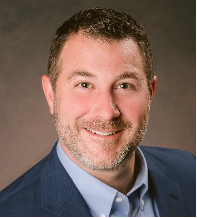
What is the rotational molding technical audit process?
Bill Christian: Audits provide a detailed, on-site evaluation of all manufacturing processes at your factory, with recommendations tailored to meet your company’s goals. An audit could address any part of your operations, including material selection, technical development, standard operating procedures, rotational molding processes, supply chain strategy, regulatory considerations, digital strategy, as well as employee safety and satisfaction. At M. Holland, when we conduct an audit of your business, we also provide materials training.
We work with our rotational molding customers to identify possible solutions to their biggest pain points, including, but not limited to, high scrap, warpage, contamination, inconsistent wall thickness, mold maintenance, secondary processes, and over- or under-cured parts.
Why should a rotational molder undergo a technical audit?
Bill: The primary consideration for a technical audit is improving operational efficiency. This can be achieved by identifying opportunities to reduce costs for you and your customers, improve profit margins and automate processes. An audit is also beneficial to molders planning to expand their capabilities to include new processes, like pulverizing and color blending. It also is useful to set KPIs and meet operational goals, from improving cycle reduction to optimizing operational flexibility.
What outcomes can rotational molders expect from a technical audit?
Bill: Molders who participate in a rotational molding technical audit will receive customized recommendations and advice to improve operational controls and increase overall cost savings. Implementing these recommendations can see improvement across several areas, including:
- Streamlined processes
- Increased production efficiency
- Improved quality
- Scrap reduction
- Lower labor costs
- Margin improvement
At M. Holland, we’ve seen firsthand the positive outcomes that come from a technical audit. Recently, we performed a new material trial for one of our rotational molding clients to test the material’s impact on the efficiency of the production process. Over the course of the trial, we were able to help the customer streamline its process by decreasing the duration of oven and cooling cycles and reducing scrap. These changes improved margins and overall product quality.
We have also helped molders identify whether they require an upgrade to their machinery. For one customer, we introduced a new material dispensing unit that provided more accurate product weight and practically eliminated material waste. The change reduced labor costs and streamlined the production process.
What does the time commitment look like? Will a technical audit interrupt business?
Bill: If done correctly, a technical audit should not interrupt business. Most evaluations will take less than a day to assess current process conditions and identify any issues or areas for improvement. We then use the information gathered during the on-site audit to create a plan to improve overall operations, which may include material sampling, process recommendations or equipment modification. Recommendations in these three areas may take longer due to necessary research and development.
Would a technical audit benefit new rotational molders?
Bill: Yes! The audit process is tailored to meet each molder’s specific requirements. For new molders, an audit would provide instruction on common processes, such as performing cure checks for bubbles in molded parts. Additionally, at M. Holland, we can include material testing for business-specific applications and impact testing to identify potential challenges that are unique to each operation.
Unlock More Efficient Rotational Molding
If you have any questions or are interested in learning more about conducting a rotational molding technical audit with M. Holland, reach out to your account manager or contact one of our dedicated Rotational Molding experts: Bill Christian (bchristian@mholland.com), Jon Hand (jhand@mholland.com) or Bryan Chance (bchance@mholland.com).
No matter if you have been in business for 20 days or 20 years, there is always room to improve rotational molding efficiency, quality and profit margins. Visit the Rotational Molding market page for more information about our expertise, services and materials.